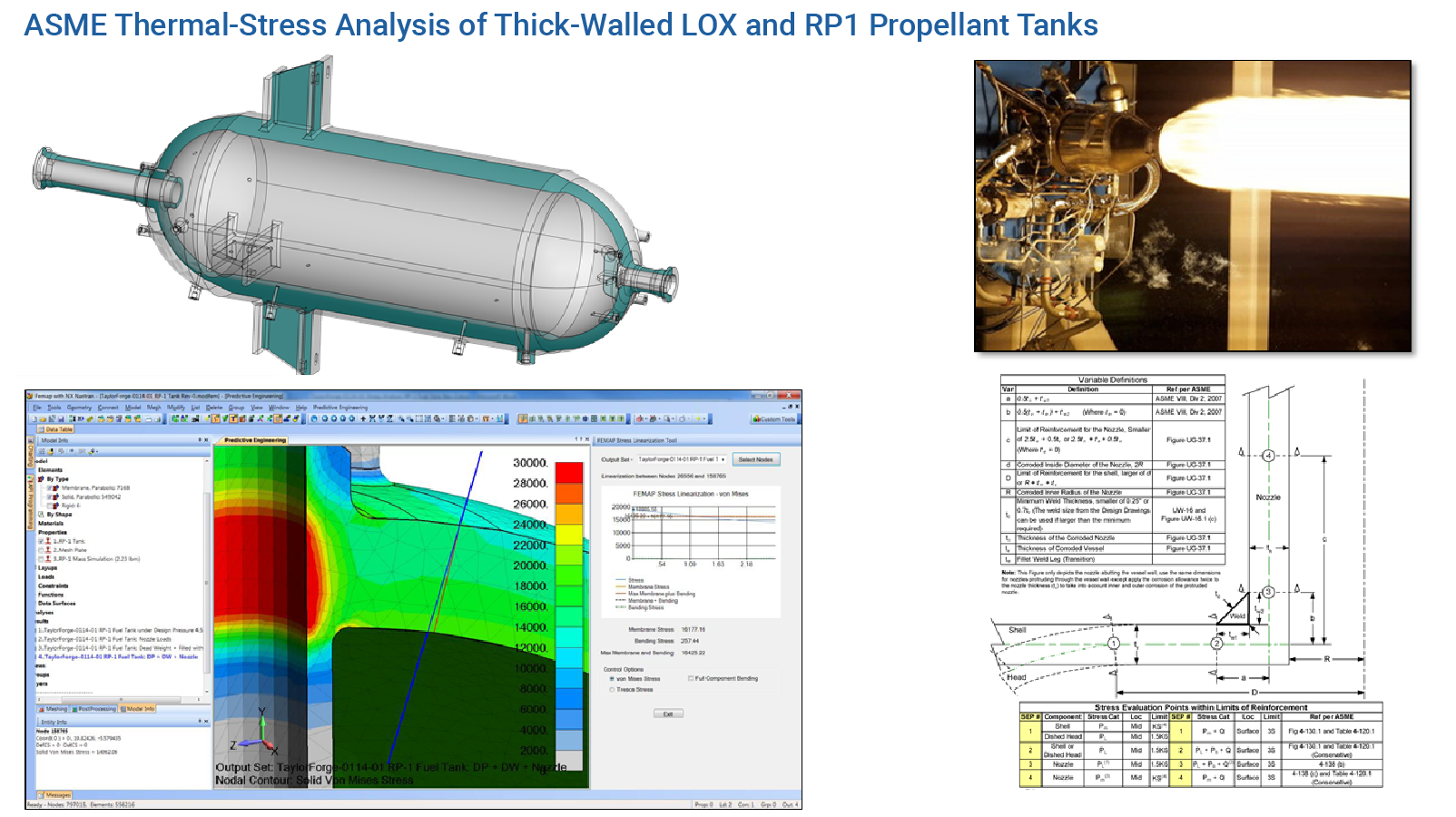
Pressure vessel closures are pressure retaining structures designed to provide quick access to pipelines, pressure vessels. Composite overwrapped pressure vessel.
A composite overwrapped pressure vessel (COPV) is a consisting of a thin, non-structural liner wrapped with a structural, designed to hold a under pressure. The liner provides a barrier between the fluid and the composite, preventing leaks (which can occur through matrix which do not cause structural failure) and chemical degradation of the structure. In general, a protective shell is applied for protective shielding against impact damage. The most commonly used composites are (FRP), using and fibers.
The primary advantage of a COPV as compared to a similar sized metallic pressure vessel is lower weight, but this may be offset by the increased costs of manufacturing and certification.
Horizontal pressure vessel in steel. Level-d The 767 Winglet Update 1.01 - Download Free Apps. A pressure vessel is a container designed to hold gases or liquids at a substantially different from the ambient pressure.
Pressure vessels can be dangerous, and fatal accidents have occurred in the history of their development and operation. Consequently, pressure vessel design, manufacture, and operation are regulated by engineering authorities backed by legislation. For these reasons, the definition of a pressure vessel varies from country to country. Design involves parameters such as maximum safe operating pressure and temperature,, corrosion allowance and minimum design temperature (for brittle fracture).
Construction is tested using, such as,, and pressure tests. Hydrostatic tests use water, but pneumatic tests use air or another gas. Hydrostatic testing is preferred, because it is a safer method, as much less energy is released if a fracture occurs during the test (water does not rapidly increase its volume when rapid depressurization occurs, unlike gases like air, which fail explosively). In most countries, vessels over a certain size and pressure must be built to a formal code. In the United States that code is the. Blu Ray Xp Driver 5 3 0 1 X86 Tablet. These vessels also require an authorized inspector to sign off on every new vessel constructed and each vessel has a nameplate with pertinent information about the vessel, such as maximum allowable working pressure, maximum temperature, minimum design metal temperature, what company manufactured it, the date, its registration number (through the National Board), and 's official stamp for pressure vessels (U-stamp).
The nameplate makes the vessel traceable and officially an Code vessel. A 10,000 psi (69 MPa) pressure vessel from 1919, wrapped with high tensile steel banding and steel rods to secure the end caps. The earliest documented design of pressure vessels is described in the book Codex Madrid I, by Leonardo da Vinci, in 1495, where containers of pressurized air were theorized to lift heavy weights underwater, however vessels resembling what are used today did not come about until the 1800s where steam was generated in boilers helping to spur the. However, with poor material quality and manufacturing techniques along with improper knowledge of design, operation and maintenance there was a large number of damaging and often fatal explosions associated with these boilers and pressure vessels, with a death occurring on a nearly daily basis in the United States. Local providences and states in the US began enacting rules for constructing these vessels after some particularly devastating vessel failures occurred killing dozens of people at a time, which made it difficult for manufacturers to keep up with the varied rules from one location to another and the first pressure vessel code was developed starting in 1911 and released in 1914, starting the. In an early effort to design a tank capable of withstanding pressures up to 10,000 psi (69 MPa), a 6-inch (150 mm) diameter tank was developed in 1919 that was spirally-wound with two layers of high tensile strength steel wire to prevent sidewall rupture, and the end caps longitudinally reinforced with lengthwise high-tensile rods.